Executives gathered at a solar conference to give pep talks about how to beat back crystalline silicon competitors, who have slashed prices and taken business away from thin-film players.
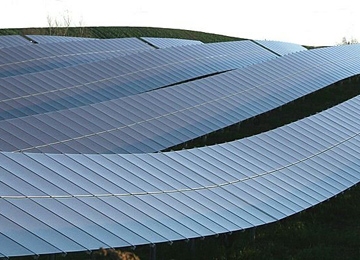
Thin-film solar developers are learning to play the offense and defense these days.
This sentiment set the tone for the first day of a conference in San Francisco Tuesday that focused on thin-film solar technologies, which use little or no silicon to produce solar cells.
These companies have been forced to refine and perhaps revise their sales pitch as they face unexpected and strong competition from makers of crystalline silicon cells and panels.
"Thin films need to use every advantage to bring electricity costs down and compete with crystalline silicon technologies," said Christian Koitzsch, a managing director of Bosch Solar Thin Film in Germany, at the Thin-Film Solar Summit in San Francisco Tuesday.
Koitzsch noted a reverse of a trend: Project developers and investors who might have given thin films serious consideration have been choosing crystalline silicon solar panels for large, ground-mounted installations instead over the past year.
It's a phenomenon that happened rather quickly. In the past year, prices for crystalline silicon solar panels worldwide have plummeted as much as 50 percent as the recession tightened its grip and Spain, which was the largest market in 2008, experienced a sharp cut in government subsidies and intensified competition in countries that offered more generous incentives.
For thin-film companies, clawing for a bigger slice of a market that is dominated by crystalline silicon solar companies is nothing new. Thin films have been in the minority because many of these companies are developing new technologies and have only recently begun commercial production.
Crystalline silicon solar panels are able to convert a higher rate of sunlight that falls on them into electricity than thin films can. The efficiencies for crystalline silicon panels mostly hover in the mid-teens, though SunPower (SPWRA) in San Jose, Calif., is producing panels with just over 19 percent efficiency.
The numbers are in the low teens for thin films – many companies are still working on jumping over that 10 percent hurdle. But thin-film developers say the materials they use could produce more electricity under low-light conditions, and their manufacturing costs could be lower.
But the price war presents a big headache, and has prompted the biggest thin-film company, First Solar (FSLR), to offer rebates in Germany, its largest market, to fend off crystalline silicon opponents (see First Solar Fears Competition From Silicon Panel Makers).
First Solar is better armed to spar with those competitors than most other thin-film companies, however. The Tempe, Ariz.-based public company is the one and only large thin-film company, and it had built up a massive manufacturing operation by the time the market demand for solar slackened.
With roughly 1-gigawatt of production capacity, First Solar is able to keep manufacturing costs low. In fact, it claims to be able to make solar panels cheaper than anyone. The 11 percent average efficiency for its cadmium-telluride solar panels also serves as a benchmark for other thin film companies.
"First Solar shows that after a critical mass in terms of production, you can demonstrate certain advantages," said Joe Armstrong, CEO of Ascent Solar Technologies, a Thornton, Colo.-based company developing copper-indium-gallium-selenide solar panels.
Ascent has a 3-megawatt pilot line, and plans to open a 30-megawatt factory in early 2010.
"We see 30 megawatts as the first demonstration of a high-volume scale manufacturing," Armstrong said. "Ten- to 30-megawatt capacity will not be sufficient to compete in cost sensitive markets."
Currently, the average selling price for crystalline silicon panels are roughly $2 per watt, and thin films need to be 25 percent cheaper to compete, said Paula Mints, the head analyst at Navigant Consulting, at the conference.
Mints' assessment didn't convince Chris Beitel, managing director of SunFab products at Santa Clara, Calif.-based Applied Materials.
"I absolutely disagree with that," said Beitel during a panel discussion at the conference. He said panel pricing is just one factor in determining the costs of installing a solar energy system. Thin-film developers and their customers could shave expenses in labor and materials for other components in the system, Beitel said.
With First Solar continuing to show sales, thin films should continue to expand their market share in the next few years, analysts say. A few startups have announced multimillion-dollar contracts over the past year. For example, Fremont, Calif.-based Solyndra, a CIGS company, has inked over $2 billion worth of contracts.
Thin-film shipments accounted for 11 percent of the global market in 2007 and 14 percent in 2008, Mints said. That share could reach around 25 percent in 2009.
Thin-film manufacturers collectively doubled their production capacity from 925 megawatts in 2007 to 2,015 megawatts in 2008, according to GTM Research. GTM Research expects the capacity to jump to 4,330 megawatts in 2009.
Manufacturers typically don't run their factories around the clock at full capacity, so the amount they actually churn out tends to be lower.
Thin-film companies are likely to produce about 2,760 megawatts this year.
Source : Seeking alpha, 2/12/09
Aucun commentaire:
Enregistrer un commentaire